Salzgitter kocht grünen Stahl
Zur Energiewende gehört die Farbe Grün. Wasserstoff soll grün sein, Erdgas soll grün sein – nun Stahl. Als seiner Ansicht erstes Unternehmen teilt das Stahlunternehmen Salzgitter AG einen wichtigen Schritt in Richtung Zukunft mit: die Herstellung von fast absolut grünem Stahl.
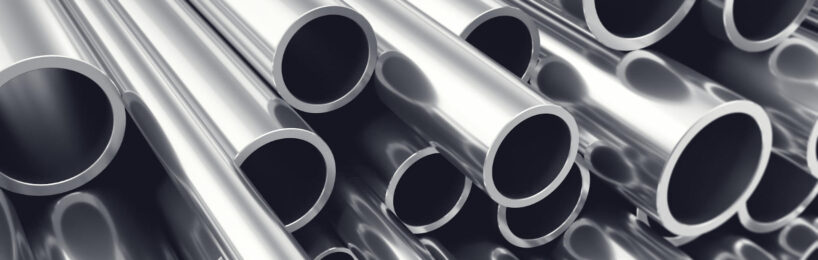
Erste Direktreduktionsanlage
Gut zwei Millionen Tonnen grünes Eisen wollen die Stahlkocher der Salzgitter AG ab 2026 jährlich herstellen. Ihre erste Direktreduktionsanlage (Direct Reduction Plant – DRP) hat die Salzgitter AG zu diesem Zweck jetzt in Auftrag gegeben. Das teilt der zweite Vorstandsvorsitzende des Unternehmens, Gunnar Groebler, auf „LinkedIn“ mit. Liefern soll sie ein Konsortium aus:
- Tenova, ein Unternehmen der italienischen Techint-Gruppe, mit Hauptsitzen in Villebon Sur Yvette bei Paris und Castellanza bei Mailand.
- Danieli-Gruppe, Buttrio (Friaul, Italien):
- DSD Steel Group GmbH, Saarlouis
Salcos für kohlenstoffarme Stahlerzeugung in Salzgitter
Die Salzgitter AG hat das Konsortium mit dem Bau der DRP auf dem Gelände der Salzgitter Flachstahl GmbH beauftragt. Wie das Konsortium mitteilt, handelt es sich bei der Anlage um das größte Teilwerk in der ersten Stufe des Transformationsprogramms Salzgitter Low CO2 Steelmaking („Salcos“). Es verfüge über eine Produktionskapazität von mehr als zwei Millionen Tonnen direkt reduziertem Eisen (DRI) pro Jahr. Das Qualitäts-DRI, das von der 2,1-Tonnen-Zero-Reformer-Anlage Energiron DR produziert wird, soll eine nachhaltige Produktion von hochwertigen Warmbandcoils in einem neuen Elektrostahl-Stahlwerk ermöglichen.
CO2-arme Stahlerzeugung am Standort Salzgitter
Die Auftragsvergabe markiere einen weiteren, entscheidenden Meilenstein auf dem Weg zu einer CO2-armen Stahlerzeugung am Standort Salzgitter und für den Salzgitter-Konzern. Angestrebt ist eine endgültige Reduzierung der Kohlenstoffemissionen um 95 Prozent. Die Salzgitter AG erhebt damit den Anspruch, Vorreiter einer nachhaltigen Industrie zu sein.
Ziel von Salcos ist es, eine nahezu CO2-freie Stahlproduktion zu eine erste von drei Stufen soll bereits Ende 2025 in Betrieb gehen. Sie besteht aus:
- einer Direktreduktionsanlage,
- einem Elektrolichtbogenofen und
- einer 100 MW Elektrolyseanlage zur Wasserstofferzeugung.
Transformation der Stahlproduktion
Bis Ende 2033 soll die Transformation der Stahlproduktion am Standort Salzgitter abgeschlossen sein, weit vor den regulatorischen Vorgaben. Das Salcos-Programm befindet sich bereits mitten in der Umsetzung. Die Finanzierung der Stufe 1 von Salcos sicherten Fördermittel der Bundesrepublik Deutschland und des Landes Niedersachsen in Höhe von insgesamt rund einer Milliarde Euro sowie durch substanzielle Eigenmittel der Salzgitter AG von einer weiteren Milliarden Euro. Zuvor war bereits ein Elektrolichtbogenofen als weitere wichtige Produktionsanlage für die CO2-arme Stahlproduktion bestellt worden. Die DRP, die größte Teilanlage im Salcos-Programm wurde nun bestellt.
Wasserstoff und Erdgas in jedem Mischungsverhältnis
Die Direktreduktionsanlage basiert auf der innovativen „Energiron ZR Direct Reduction“-Technologie, eine gemeinsame Entwicklung von Tenova und Danieli. Sie könne flexibel mit Wasserstoff und Erdgas in jedem Mischungsverhältnis betrieben werden. Die Energiron-Technologie ist ein Hybrid-Design und ermöglicht die Verwendung eines Reduktionsmittels mit der Möglichkeit, Wasserstoff bis zu 100 Prozent oder eine beliebige Mischung davon zu verwenden. Tatsächlich sei die Verwendung von etwas Erdgas während des DR-Prozesses geeignet, um ein Mindestmaß an während des Schmelzens benötigtem Kohlenstoff hinzuzufügen.
Die Technologie ist in der Lage, CO2 abzuscheiden und zu nutzen, was die gesamten Kohlenstoffemissionen der Anlage weiter reduzieren und eine zusätzliche Einnahmequelle für den Anlagenbetrieb darstellen wird.
Pneumatischer Hot-DRI-Transport zur Heißbeschickung im EAF
Die Anlage wird bereits die Hälfte der bis 2033 geplanten gesamten DRI-Kapazität bereitstellen. Er werde über das bewährte Transportsystem „Hytemp“ mit dem benachbarten Elektrolichtbogenofen (electric arc furnace – EAF) verbunden, so dass die reduzierten Eisenpellets auch von weit her heiß in den Ofen eingebracht werden können. Dies gewährleiste eine hervorragende Energieeffizienz des Gesamtprozesses. Das patentierte Hytemp-System sorge für den pneumatischen Hot-DRI-Transport zur Heißbeschickung im EAF bis 600 °C, wodurch Energieeinsparungen erzielt würden. Die Anlage werde zudem in der Lage sein, kaltes DRI zu produzieren.
Investitionsentscheidungen für Transformation
Groebler sieht sein Unternehmen als ersten europäischen Stahlhersteller, der für seine Transformation die Investitionsentscheidungen getroffen, die Finanzierung gesichert und wesentliche Aufträge vergeben hat. Ab 2026 soll die Anlage gut zwei Millionen Tonnen direktreduziertes Eisen pro Jahr produzieren. Dann werde es in der Lage sein, seinen Kunden bedeutende Mengen an grünem Stahl zur Verfügung zu stellen.
Tenova: Takgraf und Delkor
Tenova ist ein Zulieferer der Metallindustrie auch über bekannte Marken wie Takgraf und Delkor in der Bergbauindustrie. Das Unternehmen beschäftigt eigenen Angaben zufolge über 2.300 Fachleute in 19 Ländern in der Entwicklung von Technologien und Dienstleistungen zum Einsparen von Kosten und Energie sowie bei der Begrenzung der Umweltbelastung und der Verbesserung von Arbeitsbedingungen.
Danieli: Ausrüstungen für Metallherstellung
Danieli entwirft, fertigt und installiert weltweit Anlagen und Ausrüstungen für Metallherstellung, schlüsselfertig oder als Einzeleinheiten, die mit firmeneigener Technologie den gesamten Prozesszyklus abdecken, von der Erz- und Schrottaufbereitung bis hin zu fertigen Flach-, Lang-, Rohr- und Strangpressprodukten für Eisen- und Nichteisenmetalle. Die Danieli-Anlagen werden von Danieli Automation in den Bereichen Prozesssteuerung, Energie- und Instrumentierungssysteme sowie Robotik betrieben und umfassen Digi&Met-Smart-Manufacturing-Lösungen (Industrie 4.0). Eine nachhaltige Produktion gewährleistet das Unternehmen eigenen Angaben zufolge durch energiesparende Prozesse, Hybridanlagen mit erneuerbaren Energien und wasserstoffbasierte Prozesse sowie Danieli Environment-Lösungen. 10.000 Mitarbeiter sind in den Konzerngesellschaften in Italien, Deutschland, Schweden, Österreich, Frankreich, den Niederlanden, Spanien, Großbritannien, den USA, Brasilien, Thailand, Vietnam, China, Indien und Japan tätig. Ihren durchschnittlichen Jahresumsatz gibt die Danieli Gruppe mit über drei Milliarden Euro an. Die durchschnittlich Investitionen der letzten fünf Jahre in Forschung und Entwicklung belaufen sich demzufolge auf 150 Millionen Euro pro Jahr.
Kerngeschäft der DSD Steel
Die DSD Steel Group GmbH formierte sich im Jahre 2004 neu und besteht aus mittelständigen Unternehmen, die mit einer langjährigen Erfahrung auf dem nationalen und internationalen Markt tätig sind. Zum Kerngeschäft der Unternehmen gehören insbesondere die Bereiche
- Hüttentechnik
- Stahlwasserbau
- Prozesstechnik
- Korrosionsschutz
- Kraftwerksbau sowie
- Anlagen auf dem
- Energiesektor (Kohle, Wasser, Wind)
- Stahlbrückenbau
- Containerkranbau
- Stahlbau/Hochbau
- On- und Offshore.
Dezentrale Fachkompetenzen
Alle Unternehmen betätigen sich im Engineering, der Projektleitung sowie Fertigung und Montage. Die Philosophie der gesamten Gruppe ist bereits an ihrem organisatorischen Aufbau erkennbar. Die dezentralen Fachkompetenzen sind ausgerichtet auf Produkt/Marktsegmente und in unternehmerisch selbständigen Einheiten. Sie können innerhalb der Gruppe bedarfsgerecht kombiniert und erweitert werden. Dabei entstehe ein Leistungsspektrum zugunsten des Kunden, in dem das Unternehmen ein Alleinstellungsmerkmal sieht, welches ihm zufolge kein anderes Stahlbau- oder Maintenance-Unternehmen der Branche in dieser Form zu bieten habe.
Leistungen aus einer Hand
Die ständige Behauptung der Einzelunternehmen am Markt gegenüber den Wettbewerbern gewährleistet auch in der Leistungskombination eine wirtschaftliche und effiziente Lösung. Der Kunde hat in der Zusammenarbeit mit DSD, den einzigartigen Vorteil, dass er von Beginn an alle Leistungen für das Projekt aus einer Hand erhält. Synergien werden genutzt und Schnittstellen vermieden. Dabei stehen hohe Qualitäts- und Sicherheitsstandards für die gesamte DSD-Gruppe an vorderster Stelle. Gut ausgebildete und erfahrene Mitarbeiter, eingesetzt in Teams vom technischen Büro bis zur Baustelle, bilden die Grundlage des Erfolges.
Von Eisenerz zu Eisenschwamm
In der Direktreduktion wird Eisenerz mithilfe eines Reduktionsmittels in Eisenschwamm umgewandelt, der dann für die Stahlherstellung genutzt wird. Die Anlagenkonfiguration erlaubt es, Erdgas und Wasserstoff in unterschiedlichen Mischverhältnissen zu verwenden. So könne man – bei steigender Verfügbarkeit – den Anteil von grünem Wasserstoff stetig erhöhen, bis die Anlage nur noch H2O statt CO2 emittiert. Dann werde man in der Lage sein, seinen Kunden signifikante Mengen an grünem Stahl zur Verfügung zu stellen. Groebler: „Transformation braucht Zeit. Sie geschieht nicht über Nacht und ist Ergebnis harter Arbeit – ein großer Dank ans Salcos-Team! Es braucht viele Schritte und davon haben wir nun einen weiteren entscheidenden gemacht. Wir kommen dem Ziel immer näher, denn #hierpassierts!“, so Groebler in seiner LinkedIn-Mitteilung.
Pancaldi: Ergebnis einer jahrelangen Zusammenarbeit mit Salzgitter
Roberto Pancaldi, CEO von Tenova, erklärte: „Die Auftragsvergabe ist das Ergebnis einer jahrelangen Zusammenarbeit mit Salzgitter bei der Entwicklung des Salcos-Projekts, und wir fühlen uns sehr geehrt, der Konsortialführer zu sein.“ Salzgitter habe in „Energiron ZR“ von Anfang an die einzige Technologie erkannt, die entwickelt und ausgiebig getestet wurde, um einen beliebigen Anteil des reduzierenden Gasgemisches ohne Anlagenmodifikationen zu nutzen und so einen nahtlosen Übergang von Erdgas zu Wasserstoff zu ermöglichen. Darüber hinaus werde der Einsatz des Hytemp-Systems den Energieverbrauch am EAF stark senken, was wesentlich zu einer weiteren Reduzierung der CO2-Emissionen beiträgt.“
Mareschi: Leuchtturm für die Dekarbonisierung der Stahlindustrie
Giacomo Mareschi, CEO der Danieli Group: „Danieli ist stolz darauf, an der Seite der Salzgitter Flachstahl an diesem herausragenden Projekt zu sein, das ein Leuchtturm für die Dekarbonisierung der Stahlindustrie sein wird.“ Der Einsatz der Energiron-Technologie sei ein entscheidender Schritt in Richtung einer Green Steel-Ära, mit der Möglichkeit, unterschiedliche Mengen an Wasserstoff bis zu 100 Prozent als alternatives Reduktionsmittel zu verwenden, um den Kohlenstoff-Fußabdruck immer weiter zu verringern, ohne die Standard- und ausgereifte Anlagenkonfiguration zu ändern. Mareschi: „Wir setzen uns als Technologiepartner von Salzgitter voll und ganz dafür ein, dass dies ein großer Erfolg wird.“